Ultrasonic Neuromodulation
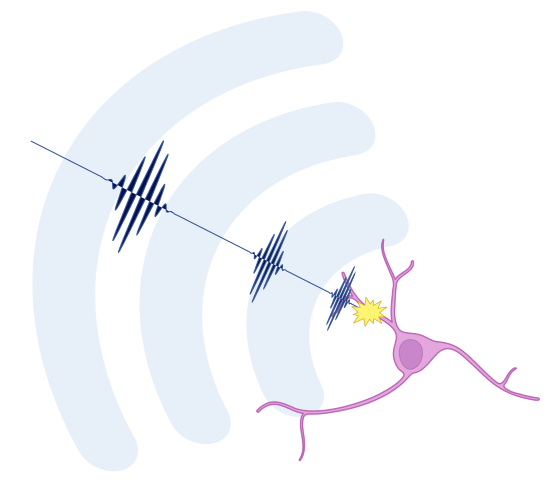
Physical Mechanisms of FUS Neuromodulation
Preclinical and clinical results are increasingly supporting the idea that low-intensity ultrasound can directly trigger cellular responses such as neuron firing, which can have downstream effects at a biological system level. This phenomenon is generating a lot of excitement for its clinical potential as a new form of precision therapy, with applications to many diseases including challenging neurological conditions. However, the physical mechanism of how the ultrasound interacts with cells in a tissue to produce these effects remains a mystery. I'm developing models along with stimulation and measurement hardware to address these open questions, in order to allow us to design effective therapies.
In Vitro Applications of LIFU
To tease apart the details of how ultrasound is interacting with cells, I've developed an in vitro focused ultrasound stimulation platform that we can use for precise stimulation of cell cultures while directly observing the cells in standard microscopy geometries. Along with collaborators in cell biology, I'm also exploring how the insights that emerge from these experiments could be adapted for use directly in cell culture, such as in stem cell differentiation or tissue engineering.
Read our review of ultrasound in tissue engineering
In Vivo Models for US Neuromodulation
In order to validate the hypotheses developed in vitro, I've developed a wearable focused ultrasound device that can be used for precision stimulation in preclinical experiments. This device can be used in vitro to concretely identify the role of specific biophysical pathways in ultrasonic neuromodulation. Beyond this, I'm using the device with collaborators for sonogenetic neuromodulation as well as to address open fundamental questions in neurobiology.
Ultrasound-Responsive Materials
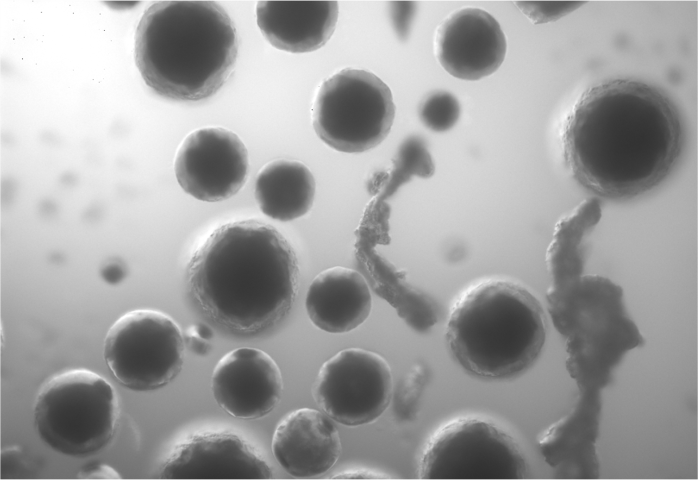
Ultrasonically Controlled Release using Antibubbles
In fields such as medicine, biology, materials science, and chemistry, it is
desirable to trigger chemical or biological processes noninvasively. To this
end, ultrasound provides advantages over conventional approaches using light,
electricity, or magnets. In addition to its high penetration depth in complex
media, ultrasound can be patterned precisely and focused into small spatial
regions. However, most ultrasonically-triggered processes to date require
high ultrasound intensities, which is undesirable in many systems because they
can trigger damaging effects such as cavitation or strong fluid flows. Recently,
I have been exploring how we can overcome these limitations using
cleverly-engineered microstructures. Antibubbles - air bubbles with a liquid
core - are one such structure that respond strongly to ultrasound. Antibubbles
can be loaded with diverse payloads and burst using low-intensity
ultrasound, making them valuable new carriers for use in ultrasound-triggered
chemical and biological processes.
Read the paper
Read our review of ultrasound-responsive materials
Microactuation
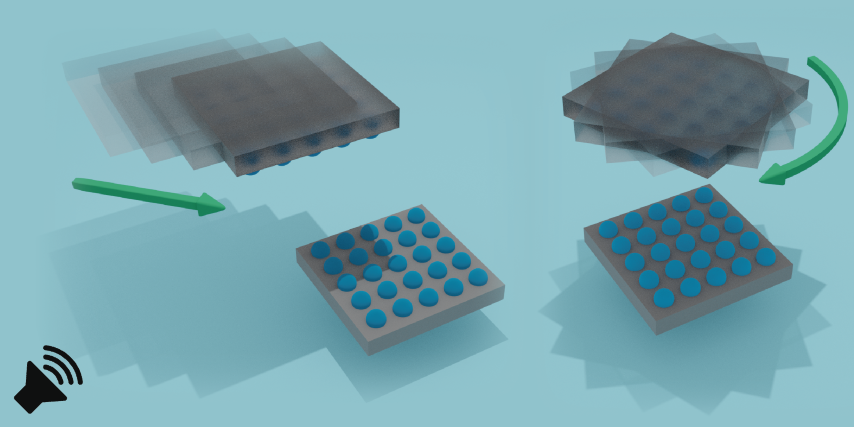
Bubble-Based Acoustic Actuation
Ultrasound can provide many advantages for non-contact manipulation of objects
in a sound field. However, there are typically constraints on the precision and
size of objects that can be manipulated given a certain wavelength of sound. One
way around these limitations is to make use of sub-wavelength scatterers, like
bubbles. In a sound field, bubbles respond strongly to sound and will exert
attractive or repulsive forces on other nearby objects or bubbles. These forces,
however, are very weak and haven't been used for large-scale actuation.
Here, we show how the forces can be amplified by patterning the bubbles into
rigid structuers. The amplified forces are strong enough to manipulate and align
centimeter-scale structures using 100-micron scale bubbles. We further show how
the bubble patterns can be modified to create an acoustic motor, generating
continuous rotation of one of the structures.
Read the paper
Media Coverage
Media Coverage (DE)
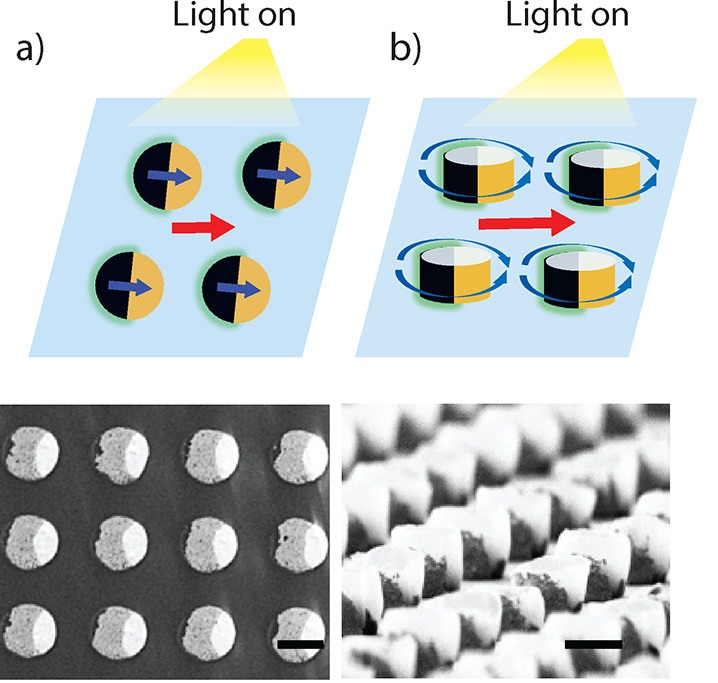
Light-Driven Distributed Pumping in Microchannels
As the size of fluid channels gets smaller, external pressure pumps need to do
more work to fight viscous friction in the channels. At the same time, in
complex fluid networks, it is difficult to locally control the flow, and the
flow profiles are effectively set at design-time. Here we introduce a new
approach to control flows in microchannels using distributed light-activated
chemical pumps. When light shines on the pumps, they generate a unidirectional
flow whose speed can be controlled by the light intensity. These micropumps
offer not only the possibility to locally support external pumps within a
microchannel, but could be used to locally change flow patterns and the flow
profile within microfluidic networks.
Read the paper
Acoustic Holograms & Field Synthesis
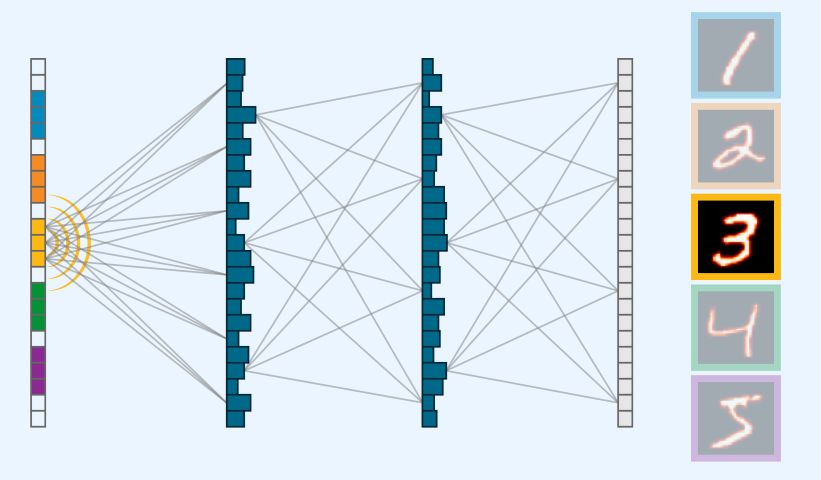
Dynamic Acoustic Holograms
Acoustic holograms are a powerful tool to shape ultrasonic pressure fields.
Holograms can project significantly more complex patterns than state-of-the-art
digital transducer arrays. Coupled with their simplicity and low cost, they
provide several advantages in diverse settings from assembly to medical
therapeutics.
One challenge for conventional acoustic holograms, however, is that once they
are fabricated, the projected field pattern cannot be changed. For applications
where real-time control over the pressure field is needed, it would be
beneficial to be able to dynamically change the fields using acoustic holograms.
Towards this end, I've worked on projects to create a spatial sound modulator,
inspired by spatial light modulators used commonly in optical devices like
digital projectors. One approach we took was to create bubbles at precise
locations that can block sound on command, producing switchable binary amplitude
holograms. Another approach I developed makes use of multiple hologram planes
coupled to a multi-source array. By turning on different elements sequentially,
multiple pre-defined fields can be projected. This technique can even be
generalized to create more sophisticated compressive acoustic projectors.
Read the paper: Multiplane Acoustic Networks
Read the paper: Bubble Sound Modulator
Acoustic Sensing
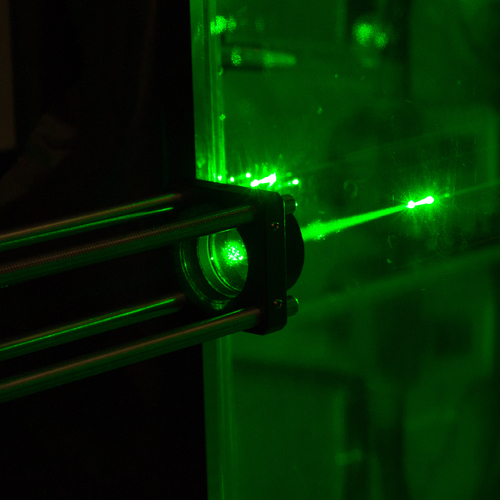
Acoustic/Elastic Sensing with Optical Breakdown Shocks
When managing ships or other ocean infrastructure, it is important to monitor
the
health
of structures and to identify unknown objects on the surface. These types of
inspection
tasks currently require significant time and money to carry out, largely because
the
relevant sensors must make contact with the inspection target. In order to
enable
faster
and more thorough inspections, I developed an acoustic sensing technique that
uses a
high-power laser to create sound at controllable points in the water, through a
process
called optical breakdown. By listening to how the short optical breakdown
pulse
scatters off of underwater objects, information about the material's composition
and
geometry can be calculated. This technique provides a new approach for
underwater
vehicles to remotely map structural and material properties along an underwater
object.
Read the paper
Medical Devices
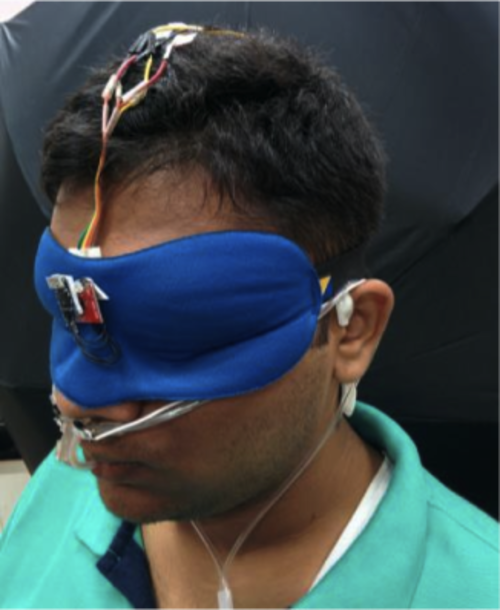
Accessible Sleep Apnea Screening Device
Between 7 and 18 million Americans suffer from sleep disordered breathing (SDB),
including those who suffer from obstructive sleep apnea (OSA). Despite this high
prevalence of SDB, existing diagnostic techniques remain impractical for
widespread
screening. Furthermore, once a diagnosis is made, there are no readily available
tools
for routine monitoring of treatment efficacy on a longitudinal basis.
As part of the ReDx initiative, I mentored a team
in
Mumbai to develop a wearable sleep mask with sensors for at-home screening and
longitudinal monitoring of patients at risk for OSA. We developed a few
prototypes
and
ran an early round of clinical testing to compare the performance of our device
with
existing at-home monitors.
Read the paper
Granular & Fluid Mechanics
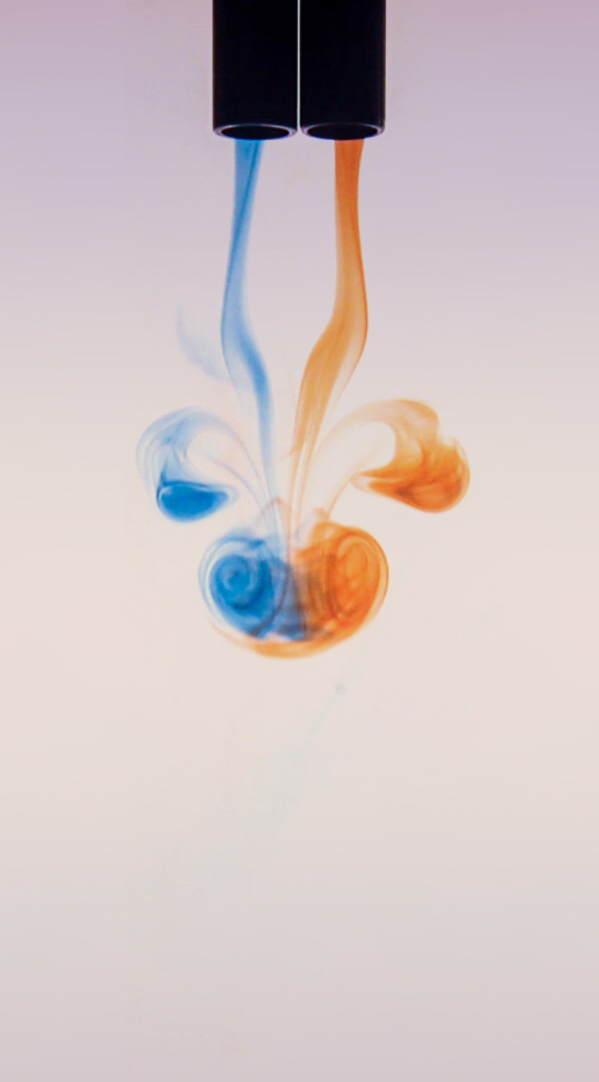
Vortex Interactions for Underwater Propulsion
Underwater robots can maneuver more precisely if they use pulsed jets instead of
propellers to generate thrust. But in situations where multiple jets are needed
-
like
when a robot needs to dock to a structure, or when a swarm of robots need to
coordinate
their activities - it is unclear how to best coordinate all the jets involved.
In
order
to design and control underwater robots for efficient motion, it is critical to
understand how the jets' wakes can interact, and how these interactions affect
the
thrusters' performance. To do this, I built an experiment to measure thruster
performance when pulsed jets are ejected simultaneously. As the jets develop,
vortex
rings are formed in the wake; when the jets are close enough, the vortex
interactions
reduce thruster performance. To explain this behavior, I developed a physical
model
that
agrees well with the data. My experiments show how some pulsing strategies can
hurt
performance, suggesting new strategies that leverage the vortex interactions to
improve
performance.
Read the paper
Outreach Video
Gallery of Fluid Motion Video
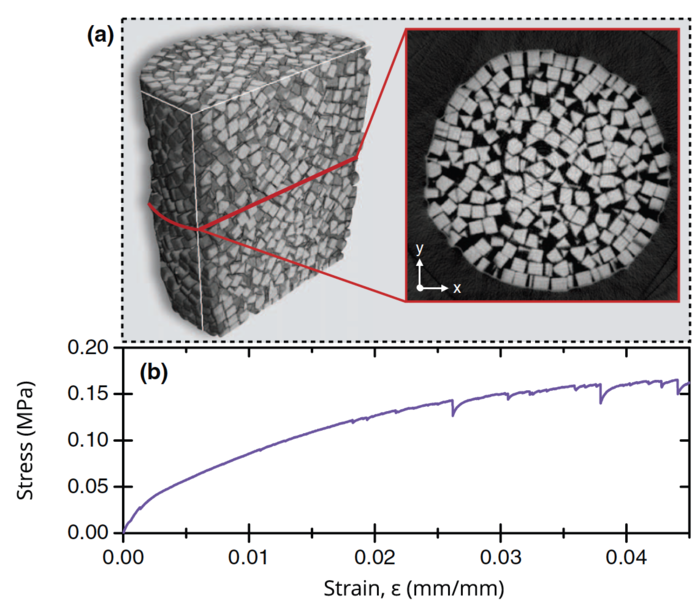
X-Ray Imaging of Granular Packings During Compression
To directly investigate how particle shape and particle interactions affect the
mechanical properties of granular packings, I designed and built an x-ray
tomography
system that is able to image the 3D details of a granular packing while it is
compressed
in an Instron materials tester. This way, a packing's mechanical response
(measured
by
the Instron) can be directly related to the internal geometry and rearrangements
of
grains.
Read the paper
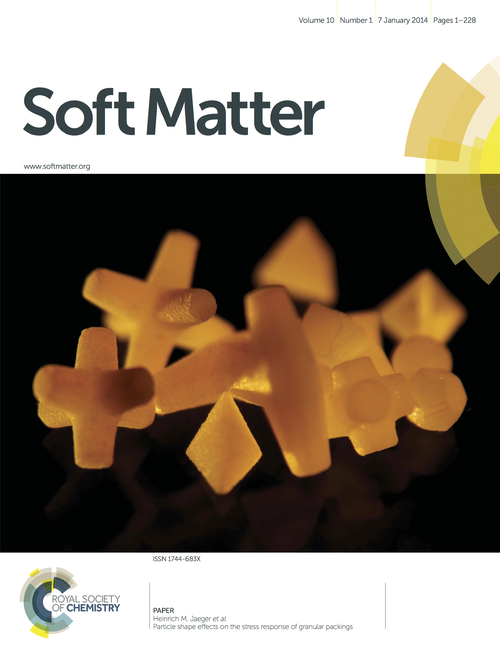
Granular Mechanics & Particle Shape
When you load a pile of sand (whether in the lab, at the beach, or on a
construction
site), the packing will slowly weaken until a slip-plane forms and the system
cannot
support the stress. However, if the shape of the grains is changed, the
packing's
behavior can change drastically, like we saw with the chains. An important
question
for
designing granular systems is how the choice of grain shape will impact the
mechanical
response. To understand this relationship, we 3D-printed tens of
thousands of
mm-scale grains in 14 different
shapes, and measured how bulk packings of each shape responded to
mechanical
compression. In addition to the broad collection of characteristic responses
that we
collected, we observed that local interactions between grains makes some
packings
more
sensitive to confining pressure, suggesting that certain shapes can provide a
more
widely-tunable response for dynamic applications.
Read the paper
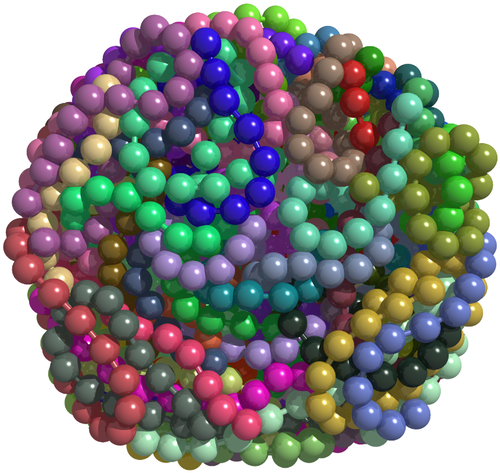
Entanglement in Granular Chains
When a pile of chains is compressed, it will sometimes exhibit the unusual
behavior
of
getting stronger the more it is compressed. This behavior is known as 'strain
stiffening.' To figure out what causes strain stiffening in chains, we collected
3D
x-ray measurements of the internal structure of chain packings at different
stages
during compression. These measurements revealed that the packings' increasing
strength
comes from interlocked clusters of chains that span the system. Moreover, if the
chains
are too short, they do not form large clusters, and we observed a corresponding
loss
of
the strain-stiffening behavior.
Read the paper